A step motor for sale is an electric motor that rotates in discrete step increments. The movement of each step is precise and repeatable; therefore the motor’s position can be controlled precisely without any feedback mechanism, as long as the motor is carefully sized to the application.Industrial applications include high speed pick and place equipment and multi-axis CNC machines, often directly driving lead screws or ballscrews. In the field of optics they are frequently used in precision positioning equipment such as linear actuators, linear stages, rotation stages, goniometers, and mirror mounts. Other uses arein packaging machinery, and positioning of valve pilot stages for fluid control systems. Commercially, stepper motors are used in floppy disk drives, flatbed scanners, computer printers, plotters, slot machines, image scanners, compact disc drives and many more devices.
Energizing a coil winding creates an electromagnetic field with a north and south pole. The magnetic field created by the winding will cause the magnetized rotor to align itself with the magnetic field, since unlike poles attract.The direction of the magnetic field can be altered to create rotation of the rotor.
Fig 1. illustrates a typical step sequence for a two phase motor. In Step 1, phase A is energized; it locks the rotor in the position shown. In Step 2, phase A is turned off and phase B is turned on, the rotor rotates 90°clockwise. In Step 3, phase A is turned on again but with reversed polarity and in Step 4, phase B is turned on with reversed polarity. This sequence completes a full turn of the rotor. Repeating this sequence causes the rotor to rotate clockwise in 90° steps. This is the basic “one phase on” stepping.
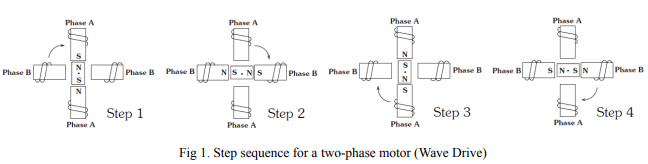
Fig 2. Shows a more common “two phases stepping motor “where both phases are always energized.The rotor in this stepping mechanism alighs itself between the poles. This stepping method gives 41.4% more torque than “one phase on” stepping but requires twice the input power.
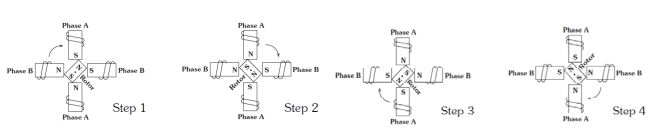